
Case Studies
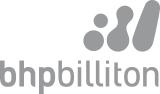
BHP Billiton
Rocky terrain leads to mobility issues. No need to reinvent the wheel, just to apply it.
The BHP Roxby Downs Copper Refinery is located at Olympic Dam in South Australia and produces copper, uranium, silver and gold.
Roxby Downs was purpose built to service the mine, which contains one of the largest known ore bodies in the world today.
The mine is entirely owned by BHP Billiton, a leading global resources company that excels in the discovery, acquisition, development and marketing of natural resources.
The problem
BHP was using a range of essential equipment that was heavy and difficult to move around the site manually without causing significant damage.
BHP workers too, were putting their safety at risk by manually handling the heavy equipment, also causing inefficiency in productivity.
The assessment
As we do with all partners, we listened to their concerns and responded quickly. We immediately booked in a site visit and conducted a site audit.
We sat down and listened to what BHP workers were concerned about, and discussed how we could help.
After observing the working processes, we devised a plan and together with our partner, we came up with an effective solution.
The Solution
Using the information gathered from our conversations and observations, we decided the best course of action was to manufacture a range of stainless steel outdoor wheels to be fitted to the bottom of the platform.
The new wheel kit improved mobility and reduced the risk of equipment damage, while providing a higher level of safety for workers.
The Result
BHP was able to move the platforms around the site easily, and still have a corrosive free product.
They had effectively solved the issue of ongoing damage to their equipment, and potential risk to worker safety was identified and addressed.
Other Branach users are now enjoying the benefits of the outdoor wheel kit too.
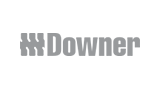
Downer
One technician. One job. Three ladders. It just didn’t add up. So we invented a new solution.
Downer is recognised as a leading provider of services to customers across a variety of industries including engineering; electrical; maintenance; technology and communication services… And a whole lot more.
Their business is focused primarily in Australia and New Zealand, however they do have a presence in the Asia-Pacific region, South America and Southern Africa.
The problem
The technicians in the Foxtel Installation Division of Downer Group typically worked alone and needed a safe access solution for a single person working at heights, while installing satellite dishes.
With Downer’s current practice, a single worker required three ladders to cover a single and double story house. The products they were using were creating issues with stability and slipping, as well as manual handling through tight domestic work sites.
The assessment
Frustrated with the inefficiency and safety risk associated with their current work system, Downer approached us looking for a completely new way of carrying out their height work practices.
We decided to spend time talking to the Downer workers directly involved in the project, to best understand the opportunities and limitations associated with the project.
We co-employed an engineer to work solely on establishing the new system, while Branach conducted safety audits, site visits and keenly observed current work practices.
Using the information obtained, we began a trial period testing products unique to Branach, ensuring height safety and efficiency was a priority.
After a number of prototypes were put to the test, we narrowed in on a solution.
The Solution
We determined the best course of action was to focus on developing an innovative product, currently unavailable in the market place.
We designed and built an extension ladder that packs down to 2.4 metres, however when deployed with two modular sections, extends up to 6.7 metres.
With a focus on height safety, we included our TerrainMaster to stabilise the ladder and prevent slipping. Our design also included an optional handrail that allows the worker to safely step on and off the roof.
The Result
Due to the complexity and high-risk nature of the project, timelines were extended as completely new innovations and work systems were required. This groundbreaking system was demonstrated to all Downer State offices and Downer contractors who would be using the system day to day. The feedback from these national stakeholders was imperative to fine-tune the system. These designs take time and care. It is not something that can be rushed as people’s lives depend on it.
Branach continue to make revisions to the product, with trials continuing across Australia, while a positive and trusting partnership with Downer was formed.
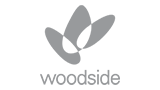
Woodside
Salt. Humidity. Tropical storms. Woodside faces often brutal conditions offshore. Our CorrosionMaster, however, loves a challenge.
As an Australian oil and gas company with a global presence, Woodside is recognised for its world-class capabilities in exploration, development and the production of liquefied natural gas (LNG).
Woodside's achievements in oil and gas are long and illustrious, underpinned by 60 years' experience. So when industry leaders go searching for a product they can rely on, they go searching for excellence.
The problem
Before partnering with Branach in 2014, Woodside were using a fleet of timber ladders to access scaffold on their rigs. Sure, using timber helped combat issues of metal corrosion caused by salt and water, but the often-brutal tropical weather lead them to rot over time.
When the timber degraded and weak points formed on the ladders, a number of the rungs failed resulting in more than a few near miss incidents, placing workers' safety at risk.
The assessment
We decided to have a look at how Woodside operated first hand. We flew across the country and boarded a rig to talk to employees about how we could make their job easier. And safer!
We watched how they went about their work and discussed potential products that would fix their issues.
After filtering through our notes and photos, it was clear that the Woodside ladders needed to be lightweight, have a load rating of 150 kilograms, not absorb water and, most importantly, be corrosion resistant.
The Solution
A solution was developed using products unique to Branach. We sent a trial fleet of CorrosionMaster FND single ladders to the rig. The all-fibreglass ladders were lightweight, sturdy and able to withstand the most challenging Woodside testing.
The trial was a huge success with all timber ladders immediately removed and replaced by 400 Branach ladders.
The Result
We were delighted to provide Woodside with a solution to a height safety issue that had troubled them for years. The result was a massive improvement in employee safety and productivity.